TZM Alaşım Üretim Süreci
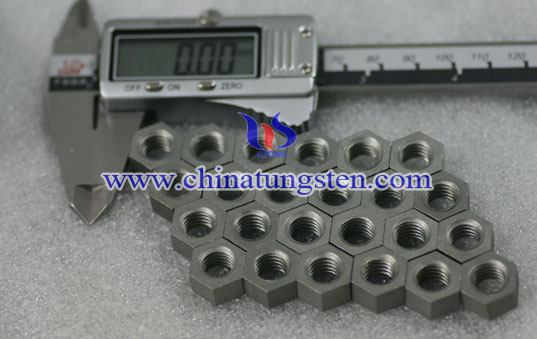
Giriş
TZM alaşımında yaygın olarak kullanılan üretim yöntemleri toz metalurjisi yöntemi ve vakumlu ark eritme yöntemidir. Üreticiler, ürün gereksinimlerine, üretim sürecine ve farklı cihazlara göre farklı üretim yöntemleri seçebilir. TZM alaşım üretim işlemleri aşağıdaki gibidir: karıştırma - presleme - ön sinterleme - sinterleme - haddeleme tavlama -TZM alaşım ürünleri.
Vakum Arkı Erime Yöntemi
Vakumlu ark eritme yöntemi saf molibdeni eritmek için bir ark kullanmak ve daha sonra belirli miktarda Ti, Zr ve diğer alaşım elementlerini içine eklemektir. İyi karıştırıldıktan sonra, geleneksel döküm yöntemleriyle TZM alaşımı elde edilir. Vakum ark eritme işleminin üretim süreci, elektrot hazırlama, su soğutma etkileri, kararlı ark karıştırma ve eritme gücü vb. Içerir. Bu üretim işlemleri TZM alaşımı kalitesi üzerinde belirli bir etkiye sahiptir. İyi bir performans üretmek için TZM alaşımının üretim süreci için sıkı gereklilikleri yerine getirmesi gerekir.
Elektrot gereksinimleri: Elektrotun bileşenleri düzgün olmalı ve yüzey kuru, parlak, oksidasyona ve bükülmeye, doğrusallığa uyum şartlarına sahip olmamalıdır.
Su soğutma etkisi: Vakum sarf malzemesi eritme ocağında, kristalleştirici esas olarak iki etkiye sahiptir: Birisi kristalleşmenin yanmayacağından emin olmak için eritme sırasında açığa çıkan ısıyı uzaklaştırmaktır; Diğeri ise TZM alaşım boşluklarının iç organizasyonunu etkilemektir. Kristalleştirici, yoğun ısıtmayı boşluğa alttan ve alttan geçerek boşlukları yönlendirilmiş sütun yapısına dönüştürür. Erime sırasında TZM alaşımı, 2.0-3.0 kg / cm2 soğutma suyu basınç kontrolleri ve yaklaşık 10 mm su tabakası en iyisidir.
Kararlı ark karıştırma: TZM alaşımı eritme sırasında kristalleştirici ile paralel olan bir bobine artı. Açıldıktan sonra manyetik alan haline gelecektir. Bu manyetik alanın etkisi esas olarak yay bağlamak ve erimiş havuzun karıştırılarak katılaşmasıdır, bu nedenle yay bağlama etkisi "kararlı yay" olarak adlandırılır. Ayrıca, uygun manyetik alan yoğunluğu ile kristalizör arızasını azaltabilir.
Erime Gücü: eritme tozu, erime akımı ve voltaj anlamına gelir ve önemli bir proses parametreleridir. Uygun olmayan parametreler TZM alaşımında eritme arızasına neden olabilir. Uygun erime gücünü seçin, büyük oranda motor ve kristalleştirici boyut oranına dayanır. "L" elektrot ve kristalleştirici duvar arasındaki mesafeyi, daha sonra düşük L değeri, kaynak havuzu için yayın kapsama alanını arttırdığı için aynı tozda havuz ısıtma durumu daha iyi ve daha aktiftir . Aksine, operasyon zordur.
Toz Metalurjisi Yöntemi
Toz metalurjisi yöntemi, daha sonra soğuk izostatik presleme işlemine tabi tutmak için yüksek saflıkta molibden tozu, TiH2 tozu, ZrH2 tozu ve grafit tozunu karıştırmaktır. Presleme sonrasında, koruyucu gaz koruması ve yüksek sıcaklıkta sinterleme, TZM boşlukları elde eder. TZM alaşımı (titanyum zirkonyum molibden alaşımı) elde etmek için, sıcak haddeleme (sıcak dövme), yüksek sıcaklık tavlama, orta sıcaklıkta haddeleme (ara sıcak dövme), kabartma stresine orta sıcaklık tavlama, sıcak haddeleme (sıcak dövme) işlemek için Boş. Dövme (dövme) işlemi ve müteakip ısıl işlem, alaşımın özellikleri üzerinde önemli roller oynamaktadır.
Ana üretim prosesleri şöyledir: karıştırma → bilyalı öğütme → soğuk isostatik presleme → hidrojen veya diğer koruyucu gaz vasıtasıyla → yüksek sıcaklıklardaki sinterleme → TZM boşlukları → sıcak haddeleme → yüksek sıcaklık tavlama → orta sıcaklıkta haddeleme → orta sıcaklık tavlama Stres → sıcak haddeleme → TZM alaşımı.