TZM Alloy Production Process
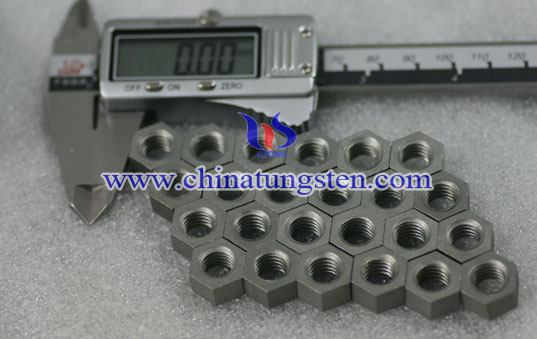
Introduction
TZM alloy commonly production methods are powder metallurgy method and vacuum arc melting method. Manufactures can chose different production methods according to product requirements, production process and different devices. TZM alloy production processes are as follows: mixing - pressing – pre-sintering - sintering – rolling-annealing -TZM alloy products.
Vacuum Arc Melting Method
Vacuum arc melting method is to use an arc to melt pure molybdenum and then to add a certain amount of Ti, Zr and other alloying elements into it. After well mixing we obtain TZM alloy by conventional casting methods. The production process of vacuum arc smelting includes electrode preparation, water cooling effects, stable arc mixing and melting power and so on. These production processes have a certain impact on TZM alloy quality. In order to produce good performance TZM alloy should to carry out stringent requirements on production process.
Electrode requirements: the ingredients of electrode should uniform and surface should be dry, bright, no oxidation and no bending, straightness compliance requirements.
Water cooling effect: in vacuum consumable smelting furnace, crystallizer effect mainly two: one is to take away the heat released during melting, to make sure that crystallization will not be burned; the other is to affect the inside organization of TZM alloy blanks. The crystallizer can pass the intense heating to the blank form the bottom and around, making blanks to produce oriented columnar structure. TZM alloy during melting, cooling water pressure controls in 2.0 ~ 3.0 kg / cm2, and the water layer at about 10mm is the best.
Stable arc mixing: TZM alloy during melting will plus a coil which is parallel with crystallizer. After power on, it will become a magnetic field. The effect of this magnetic field is mainly to bind arc and to solidify the molten pool under stirring, so the arc binding effect is called "stable arc." Furthermore, with suitable magnetic field intensity can reduce crystallizer breakdown.
Melting power: melting powder means melting power current and voltage, and it is an important process parameters. Inappropriate parameters can cause TZM alloy smelting failure. Select the appropriate melting power is largely based on motor and crystallizer size ratio. The "L" refers to the distance between the electrode and the crystallizer wall, then the lower L value, the greater the coverage area of the arc for weld pool, so at the same powder, the pool heating state is better and is more active. On the contrary, the operation is difficult.
Powder Metallurgy Method
Powder metallurgy method is to well mix high purity molybdenum powder, TiH2 powder, ZrH2 powder and graphite powder, then to process cold isostatic pressing. After pressing, sintering at protective gas protection and high temperature obtain TZM blanks. The Blank to process hot-rolling (hot forging), high-temperature annealing, intermediate temperature rolling (intermediate temperature forging), intermediate temperature annealing to relief stress, warm rolling (warm forging) to obtain TZM alloy (titanium zirconium molybdenum alloy). The rolling (forging) process and subsequent heat treatment plays significant roles on the properties of alloy.
The main production processes are as follows: mixing→ ball milling →cold isostatic pressing→through hydrogen or other protective gas→sintering at high temperatures→TZM blanks→hot rolling→ high-temperature annealing→intermediate temperature rolling→intermediate temperature annealing to relief the stress→warm rolling →TZM alloy.