TZM Hot Runner Injection Moulding
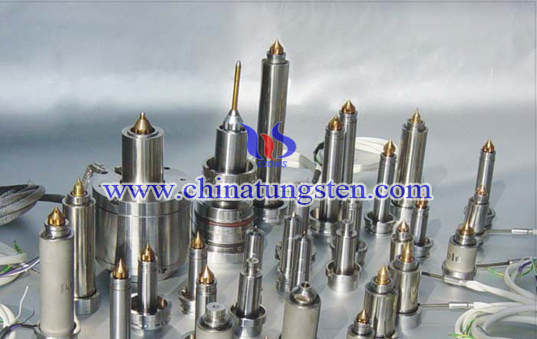
Introduction
Hot runner injection molding is a molding method, it make plastic at high temperature to inject plastic into cavity, after cooled and solidified to obtain a molded product. TZM Hot runner injection molding having high efficiency, accuracy, and other advantages, are widely used in complex shape, large quantity plastic parts production. The processes of hot runner injection molding can be divided into six stages: mold assembly, injection, packing, cooling, opening mold, products.
Classification
In hot runner injection moulding, it can be divided into cold runner injection moulding and hot runner injection moulding. According to different production cost requirement and technology requirement, we can chose different injection moulding types.
A hot runner injection moulding is an assembly of heated components used in plastic injection molds that inject molten plastic into the cavities of the mold. A hot runner system usually includes a heated manifold and a number of heated nozzles. The main task of the manifold is to distribute the plastic entering the mold to the various nozzles which then meter it precisely to the injection points in the cavities. Besides, it can reduce production cycle and for larger quantity products production.
On the other hand, cold runner injection moulding is simply a channel formed between the two halves of the mold, for the purpose of carrying plastic from the injection molding machine nozzle to the cavities. Each time the mold opens to eject the newly formed plastic parts, and the material in the runner is ejected as well, resulting in waste. If you don’t have high requirement on product’s quality and use for small quantity products production, you can chose cool runner injection moulding.