Molybdenum Glass Melting Electrode Coating
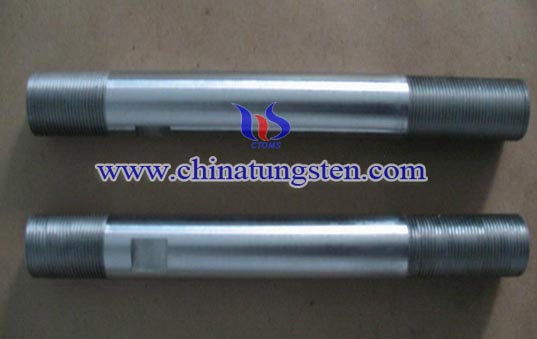
Introduction
Molybdenum glass melting electrode, having good mechanical properties, high temperature property and corrosion resistance property, is commonly used in glass furnace for glass production. However, molybdenum electrode is easily oxidized, when the temperature reaches 750℃, will produce MoO3 yellow smoke, not only worsen operating environment, but also seriously affected the life of the electrode and the glass furnace.
In order to improve molybdenum electrodes easily oxidization at high temperatures, producers invented a novel glass substrate oxidation coating. The coating uses Cr2O3 as insoluble filler, adding organic binder, using pine oil as solvent, to obtain suspension. Then using brushing method applies in molybdenum electrode surface. Compared with vacuum or inert gas processing technology, CVD technology and solid powder infiltration method, brushing method is simply and good protective effect.
Glass substrate oxidation coating main component is some metal oxide which has better high temperature properties, and the nature is oxidation protective coating. In the manufacturing, the temperature is change, so manufacturers usually chosen silicate as a main component for oxidation coating production. Because it has high temperature resistance property, and the viscosity changes slowly with temperature increase. In order to improve coating material performance will add insoluble oxides such as Cr2O3, TiO2, Al2O3, ZrO2, and so on, so coating material also calls glass-ceramic coating.
The Advantages of Coted Molybdenum Electrode
Coated molybdenum glass melting electrode has the following four advantages: Overcome the shortcoming of easily oxidized, to prolong the service life. Coated molybdenum electrode coating can use with cold installment method, without taking any measures to prevent oxidation during operation. Coating can improve molybdenum electrodes improve erosion resistance property to extend electrode life. In the production process can prevent inner molten glass decreased too faster, resulting in the possibility of the electrode exposed in air to oxidize.