Molybdenum Glass Melting Electrodes
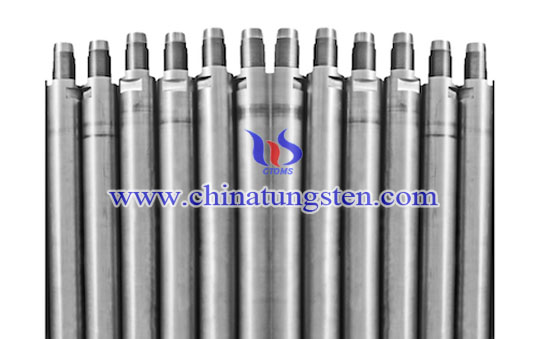
Introduction
Molybdenum glass melting electrodes surface showing the bright silver-white metal color, placed at room temperature in air, will turn dark silver or uniform gray. The higher the purity of molybdenum electrodes the colors look better and smaller annual variation. Molybdenum electrodes according to the processing methods can be divided into: polished molybdenum electrode, ground molybdenum electrode and caustic wash molybdenum electrodes. Molybdenum electrodes after polished the surface will show rendering brown or dark brown color, but this is not the color of molybdenum oxide, which is the color of impurities comprehensive oxides in molybdenum. The light brown color showing the surface uniformity is better, and then the quality is high. Conversely, if the surface is black, and different shades of color, then the poor quality of the electrode. Good quality molybdenum electrodes work in glass melting furnace for a few months the surface remaining silvery white color.
Molybdenum Electrode Quality Affected Glass Property
Molybdenum electrodes is one of the important factors affected the color, transparency of glass, so during molybdenum electrode production should strictly control the impurity and density of electrode. Iron, nickel, cobalt and other metal or metal compound in molybdenum electrodes is the main reason for colored on glass. When the iron content is more than 150PPM, glass surface will have obvious glass sense. If incubated for 48 hours can obtain green glass. In addition, the impurities of iron and nickel will reduce the life of molybdenum electrodes. Nickel and iron in electrodes mostly exists by single or multiple metal compound solid solution, and their melting point is much lower than the melting point of molybdenum and glass, so at high temperatures these impurities will melt into molten glass, resulting glass molybdenum electrodes over early erosion, reducing the effectiveness of the electrode, and affect the quality of the glass.
Molybdenum electrodes’ density will cause a certain impact on the quality and life of the glass and the electrode, which is the main factor to generate micro-bubbles in the glass. To obtain high density molybdenum electrodes should process continue finish forge, and surface does not to polish for straight and can make sure diameter scale. Density distribution main refers to radial distribution. Central part density of the electrode is generally less than the peripheral portion and the difference is between 2-5%. If the difference large will cause molybdenum electrode excessive erosion, resulting in a large number of micro molybdenum particles will go into glass affecting glass quality.