Industrial molybdenum Oxide Production Processes
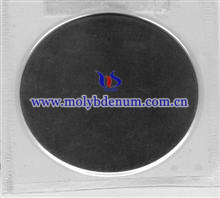
Industrial molybdenum oxide production processes are relatively simple and it is mainly used rotary kiln or hearth furnace roasting molybdenum concentrate to obtain. In the production process, the layout in the reaction vessel after filtration will be taken a part of layout into high temperature autoclave. This cycle liquid can provide a lot of heat to the autoclave, so to ensure the required heat in the kettle. Besides, during the exothermic reaction, the oxygen content of autoclave will reach 2MPa, during this time the majority of molybdenum concentrate was oxidized to molybdenum trioxide.
Its production processes are as follows: To use containing Mo 53.7%, Cu 1.2%, Fe 1.7%, S 38.8%, H2O 3.80%, oil 2.1%, -400 mesh particle size accounted for 35.2% of molybdenum concentrate as a raw material, it is slurried to 15% solids, at 240 ~ 250 ℃ oxidizing for 90min. After filtration, some parts of filter liquor will turn back to surge tank. After high pressure oxidation, the slurry is filtered, washed and dried to obtain the filter cake, and then to obtain molybdenum trioxide. The compositions of molybdenum oxide are as follow: Mo 63.1%, Cu 0.015%, Fe 0.3%, S 0.04%, molybdenum recoveries rate 99%.
molybdenum oxide obtained by roasting method, the compositions of molybdenum oxide are as follow: Mo 57%, Cu 0.25%, Fe 0.5%, S 0.1%, P 0.05%, Sn 0.05%, Sb 0.04%, molybdenum recoveries rate 97% to 98%. And some of molybdenum oxide contains S 0.15%, the molybdenum recoveries is less than 96%.
If you have got any question or inquiry regarding molybdenum, please feel free to contact us by email: sales@chinatungsten.com, sales@xiamentungsten.com or by telephone:86 592 512 9696/86 592 512 9595.