Molybdenum Disilicide Manufacturing Technique
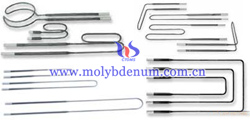
Molybdenum disilicide manufacturing technique includes ingredients, pressing, sintering, welding, shaping, testing and packing and so on. Molybdenum silicon rod has good high temperature oxidation resistance and chemical stability, so often used as heating element used in various high temperature furnaces and heating equipment. Molybdenum disilicide is a semi-metal semi-ceramic material and it not only has excellent metal properties, but also has ceramic brittle, so during manufacturing, transportation and installation process have to be careful to keep it from crumbling.
Molybdenum disilicide manufacturing processes are as follows:
1. Added 1~10 parts by weight of Mo powder, 1~10 parts by weight of W powder and 0.5~15 parts by weight of C powder into 80-99 parts by weight of molybdenum disilicide powder after mixed can obtain mixed powder.
2. Mixed 1-15 parts by weight of polyethylene glycol and 0.5-15 parts by weight of polyacrylamide and then added 70-97 parts by weight of water for diluted can obtain aqueous solution of polyethylene glycol and polyacrylamide;
3. In the mixed powder added aqueous solution of polyethylene glycol and polyacrylamide can obtain mud;
4. Put the mud in vacuum deairing machine for vacuum pressing. After molding, in sintering furnace at 1400-1700 ℃ to sinter 0.5-3 hours, at 1000-1700 ℃ in air furnace to heat 1-3 hours can obtain high-quality silicon molybdenum rod.
5. After sintering, the finished step is welding, shaping, testing and packing and so on.
If you have got any interest in molybdenum metals, please feel free to contact us by email: sales@chinatungsten.com, sales@xiamentungsten.com or by telephone:86 592 512 9696/86 592 512 9595.
Related Links: Molybdenum News & Prices