Molybdenum Disilicide Surface Problem
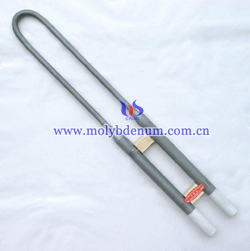
Molybdenum disilicide surface problems will affect its service life. It is long-term used in high temperature (more than 1600 ℃) and the surface will be affected and shows "bubble" phenomenon on the surface to break the SiO2 oxide film, thereby reducing the service life it.
Detailed analysis of molybdenum disilicide surface issues to improve its service life has great significance. There are many reasons for "bubble" phenomenon.
1. Sintered incomplete, from the fracture picture we will know the MoSi2 grains in matrix is not incomplete combination and the glass phase shows irregular shape with interconnection. This structure is not conducive to use in high temperatures, because it will cause the surface protective film becomes thick and has loose structure, reducing high temperature oxidation property and service life.
2. Weld defects, weld defects including incomplete weld, weld cracks and voids and so on, these defects can make the matrix of welded portion broke and the glass phase will escape form the matrix due to local overheating during electricity, generating bubbling phenomenon. Further, the welding current selection during heat and cold junctions welding will have some impact on surface.
3. Excessive iron impurities, excess iron content will break dense SiO2 protective film and appears bubbling phenomenon on the surface.
4. Cold junction defects, the size of cold junction is twice than the hot junction, so it needs longer sintering time and the higher sintering temperature. If sintering process is inappropriate making the cold junction sintering incomplete, result in the cold junction conehead showing bubbling phenomenon.
To prevent bubbling phenomenon, during molybdenum disilicide manufacturing should pay attention to the following points:
1. To select reasonable sintering process, when the material sintered at high temperature, the grains is coarse and the flexural strength is low, but low sintering temperature, sintering time will be extended so that the structure is sintered incomplete.
2. To select the appropriate welding process protect the matrix of weld portion from destroy.
3. To ensure the quality of the cold junction to prevents bubbling shows on conehead.
4. To improve the purity of raw materials reduces iron impurities.
5. To strictly control Na + and K- content in bentonite increases the softening point of the glass phase.
6. Molybdenum disilicide surface should usually do some load test.
If you have got any interest in molybdenum metals, please feel free to contact us by email: sales@chinatungsten.com, sales@xiamentungsten.com or by telephone:86 592 512 9696/86 592 512 9595.
Related Links: Molybdenum News & Prices